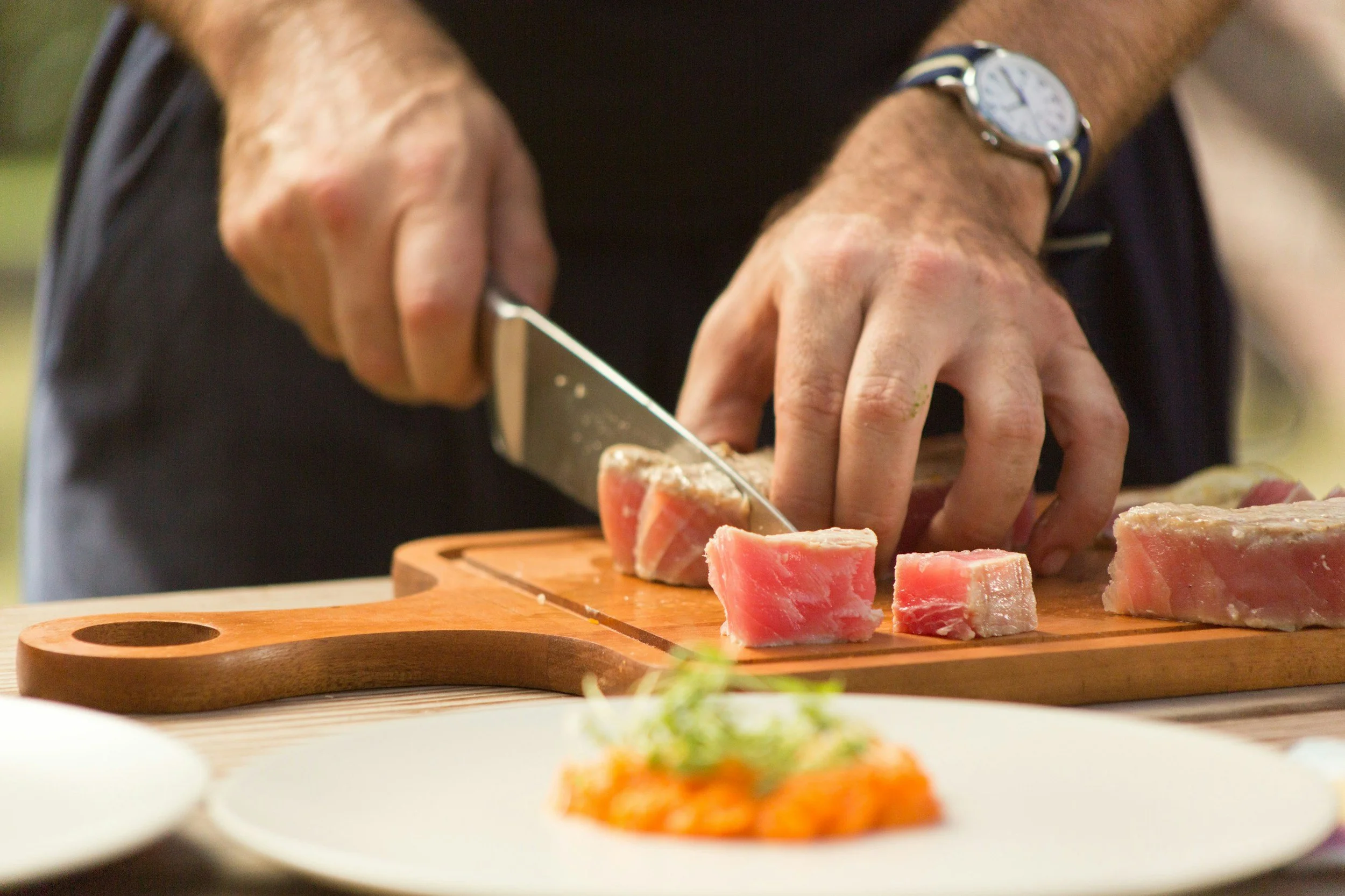
Safety Chef Knife [AHA]
(Project Duration: 1 week)
Dull blades, accidental cuts from reaching into a cluttered kitchen drawer organizer, misplaced retro-fit blade guards — this was to the call to action for a fully integrated solution that addressed blade protection, user safety, and convenience for standalone chef knife use.
[This project is part of the ‘AHA’ series — quick product development sprints based on observations about common products around us and ideas for how to make them better.]
-
Safety Chef Knife [AHA]: Design Overview
The Safety Chef Knife retains all the characteristic design elements of a traditional western style chef knife — a full-tang drop point blade with a curved ‘belly’ contour, ample blade height at the heel, and an integrated handle bolster for stability and support. While delivering all these familiar features, the Safety Chef Knife also provides the ability to swiftly sheath the blade edge in a pinch via an integrated blade guard (with an action similar to that of a folding knife) for storage, transport, or protection between food prep tasks.
Relevant Skills: Industrial Design, Product Development, Design for Manufacturing (DFM), Functional Prototyping & Testing, User Research & User-centered Design, CAD, Mechanical Design -
Safety Chef Knife [AHA]: Mechanical Design
The integrated blade guard of the Safety Chef Knife is secured to the knife’s tang via a through-hole at the blade’s heel and pivots about a spring loaded assembly pin — this pin can be pulled to remove the guard completely from the knife for ease of cleaning (guard release mechanism illustrated further below). A thumb tab was integrated into the guard geometry to allow for single-handed operation (closing/opening) of the guard.
Relevant Skills: Industrial Design, Product Development, Design for Manufacturing (DFM), Functional Prototyping & Testing, User Research & User-centered Design, CAD, Mechanical Design -
Safety Chef Knife [AHA]: Development Sketches
Development sketches illustrating exploration of the blade guard design. The main design challenge was to preserve the proportions of a traditional chef knife along its length — blade:handle (~6:5), while sufficiently concealing the guard within the handle in its closed state. A simple mechanical pivot was selected for the method of actuating the guard, resulting in the exposed portion of the guard making up 1/12 of the total knife length. It was verified through ergonomic and use-case testing that this outjutting portion of the guard would not effect or hamper usability.
Relevant Skills: Industrial Design, Product Development, Design for Manufacturing (DFM), Functional Prototyping & Testing, User Research & User-centered Design, CAD, Mechanical Design -
Safety Chef Knife [AHA]: Development Prototypes
Development Prototypes (Bottom to Top): [A] Ergonomic Chipboard Sketch Model, [B] V.1 3D-printed Prototype, [C] V.1.1 3D-printed Prototype
Relevant Skills: Industrial Design, Product Development, Design for Manufacturing (DFM), Functional Prototyping & Testing, User Research & User-centered Design, CAD, Mechanical Design -
Safety Chef Knife [AHA]: Design Overview (Cont.)
Section views of the Chef Safety Knife CAD revealing full tang blade design and prototype assembly hardware (binding barrels + machine screws) — likely to be replaced by cutlery rivets in a production design.
Relevant Skills: Industrial Design, Product Development, Design for Manufacturing (DFM), Functional Prototyping & Testing, User Research & User-centered Design, CAD, Mechanical Design -
Safety Chef Knife [AHA]: Development Sketches (Cont.)
Development sketches illustrating the guard release mechanism — a simple spring-loaded pin that indexes the guard assembly with the knife body. Due to tendency of kitchenware to harbor bacteria and accumulate and food debris, hygiene and product sanitization were primary design drivers. Ease of disassembly, ease of cleaning, and dishwasher-compatibility were factors addressed in assembly design to mitigate cross-contamination and debris build-up during the product’s use. (*Replacement of the compression spring with a flat spring, or a compliant unibody spring/guard design are future considerations for further simplifying the design for contamination/build-up avoidance).
Relevant Skills: Industrial Design, Product Development, Design for Manufacturing (DFM), Functional Prototyping & Testing, User Research & User-centered Design, CAD, Mechanical Design